TRACT C SOIL & HISTORY ANALYSIS
NEW HAVEN, CT
As part of the redevelopment of 201 Munson Street, TPA undertook a separate study of the site's industrial uses to better understand its impact on soil remediation and historic resources.
In its heyday, Winchester Repeating Arms Company's comprised over 75 acres of development including rolling mills, cartridge factories, a shot production tower, machine shops, blueing facilities, gun stock manufacturing shops, inspection and testing buildings, offices, firing ranges, warehouses, fire protection infrastructure, and power plants. Tract C was unusual in that it was lightly developed, cleared of vegetation but with only a few single-story buildings built on it. Intensive use of the site began in 1915 when Winchester grow exponentially to fulfill contracts associated with armaments for World War I.
TPA reviewed original fire insurance mapping for the complex which showed that Winchester used the land as a delivery and laydown area for raw materials. This included coal for its power plants, lumber for gun stocks, brass for ammunition, and copious amounts of primer reagents for ammunition production. A siding from the Northampton division of the New York, New Haven, and Hartford Railroad connected Winchester to its suppliers. Wooden sheds along Munson Street held the less volatile materials. Flammable and explosive material sheds were located in the middle of the site and surrounded by a twelve-foot high soil berm to prevent the risk of damage to nearby worker housing in the event of an accident. Concrete archways with locking gates allowed workers to move munitions and materials in and out quickly.
​
Several nearby buildings were used for the assembly of cartridges. Reagents were mixed on-site, packed into cartridges, and painted with mercury fulminate activate the firing pins in Winchester's patented center-fire rifles. A small lab attached to the building could provide special primer mixes for tracers and other wartime applications.
An underground network of tunnels supplied the complex with power, heat, and other utilities. Running between major buildings and with occasional manholes in between, maintenance technicians could quickly track down and repair any problems in the distribution network.
​
Production on the site quieted down after World War I as the economy returned to civilian sporting arms. A similar flurry of activity emerged again in the early 1940s with World War II. Winchester’s parent company, the Olin-Mathieson Chemical Corporation, redeveloped the site in the early 1960s for the production and handling of specialty commercial chemicals. United Nuclear Corporation leased several building in the complex and conducted radioactive research in a building abutting the site.
​
Olin exited New Haven operations in 1980, and the site was left abandoned. Trees and other vegetation began reclaiming the open lawns, berms, and parking lots. Former employees continued gun manufacturing operations in other areas of the complex as US Repeating Arms through 2006 when production was shifted elsewhere in the United States.
​
In Fall 2017, the Olin-era chemical facilities were abated and demolished. Two (2) Winchester-era munitions bunkers were documented with guidance from the State Historic Preservation Office. TPA also surveyed and documented the condition of the remaining portion of the utility corridor tunnel.
Special permission was obtained to haul in and stockpile approximately 19,000 cubic yards of clean fill for use in remediating the site. A significant construction project nearby was generating large volumes of material, and the developer was eager to take advantage of its availability. TPA planned the haul route with input from the City and monitored placement and stabilization of the stockpile.
In consultation with the environmental engineer, TPA prepared a recommendation for soil management during redevelopment. The multi-step framework adheres to the requirements of the Remedial Action Plan (RAP), prevents cross-contamination of clean fill material, and minimizes the need to export contaminated soil. Modeling of existing and proposed grading surfaces was done to confirm that the cutting and filling of soils mentioned in the RAP would result in a balanced, buildable site for future development.
​




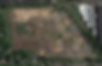
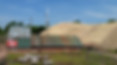